Simulating Pharmaceutical Mixers
In many practical cases diligent simulation engineering includes a validation or qualification process to ensure suitability of the chosen simulation approach for a particular setting. This is not only, but especially, true in the pharmaceutical industry with its high standards for safe conduct and strict standards that are constantly checked by regulatory authorities. Here we show how we approach this issue with the example of a mixing vessel.
The first step in such a validation process - and basically in any simulation - is to determine the exact issue that needs to be described by the simulation. It is a big difference whether the simulation needs to predict mixing time (e.g. dissolving salt, homogenizing a suspension), shear stresses (for many biogenic substances), wall attrition or spout formation and gas intake. Yet all of these may be part of a regulatory requirement and therefore need to be controllend, for example when the production is increased or parts that are no longer available need to be replaced by the engineering team.
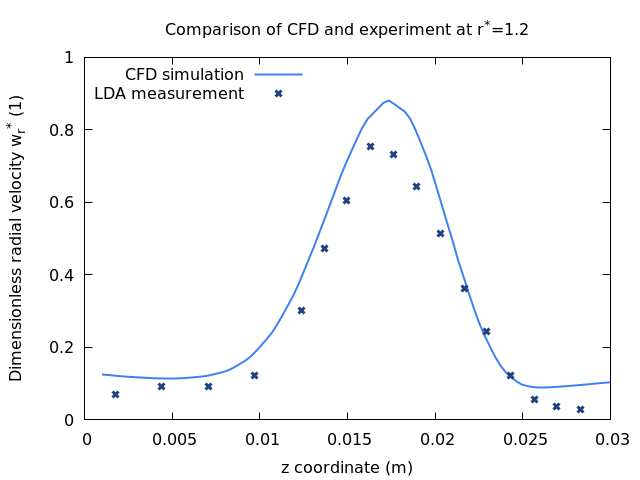
When a suitable simulation model has been selected, we start to look for published, peer-reviewed literature containing data that can be compared with our simulation. Lacking published literature we also design and conduct our own experiments. Once the data has been found or generated, the experiment is reproduced in the virtual simulation environment. By fine-tuning the often dozens of parameters that influence a simulation we identify the exact settings that are able to predict the results of the experiment (scroll down for an example). The process is more involved than I describe it here, with checking of robustness, upper and lower limits, cross checking with different sources etc. but essentially that’s the gist of it. The image shows the comparison of a tuned simulation and published measurements.
Only when a suitable mathematical simulation model and the proper set of parameters has been identified, it is possible to run the actual predictive simulations to yield results with high confidence. Over time and for many cases, we already do know the best models in which case - depending on the needed level of rigor - this first part can be omitted. Especially for the pharmaceutical industry, we also offer extensive documentation including version control, full software source code, human readable result files and more to make compliance processes as transparent as possible.
So when it is time to replace that old propeller that has been in service the last couple of years, or business is going well and you need a bigger tank: Save your engineers some headaches planning expensive and laborious physical validation processes and let us conduct the tests in our virtual laboratory! It’s faster, easier and will save you a bunch of money!
A concrete example from one of our customers:
Experimental validation of simulated mixing times
A renowned, international customer from the pharmaceutical industry granted us permission to show the following comparisons. The task was to create a CFD simulation model that predicts the dissolution of a salt in water for injection (WFI). Once the CFD model successfully duplicates the experiment (using different stirrers and rotation speeds) with sufficient accuracy, the same simulation approach was used to predict the salt dissolution for other stirrers. This ensures that the overall mixing behavior remains unchanged while allowing engineering the freedom to modernize the equipment. Once a suitable mixer (vessel) and corresponding rotation speed has been identified, a different CFD model can be used in a similar manner to ensure that critical shear rate values are not violated.
The following graphs show comparisons between experiment (red) and simulation (blue) for different stirrers and rotational speed. All simulated values are within the margin of error of the measurements.
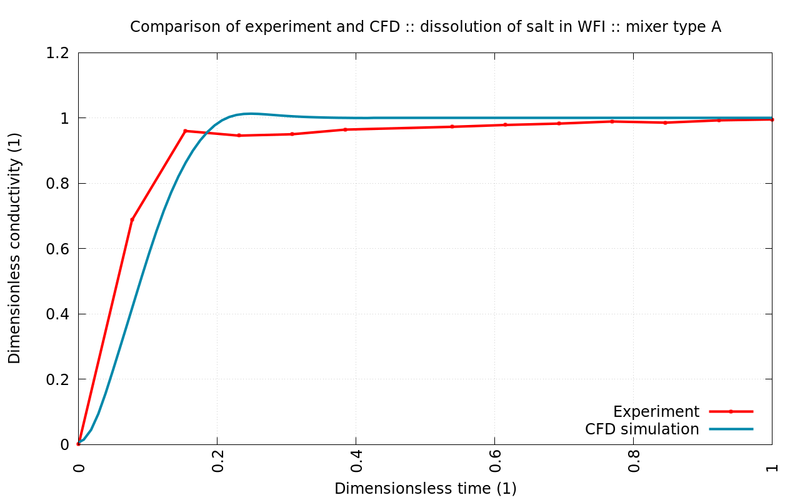
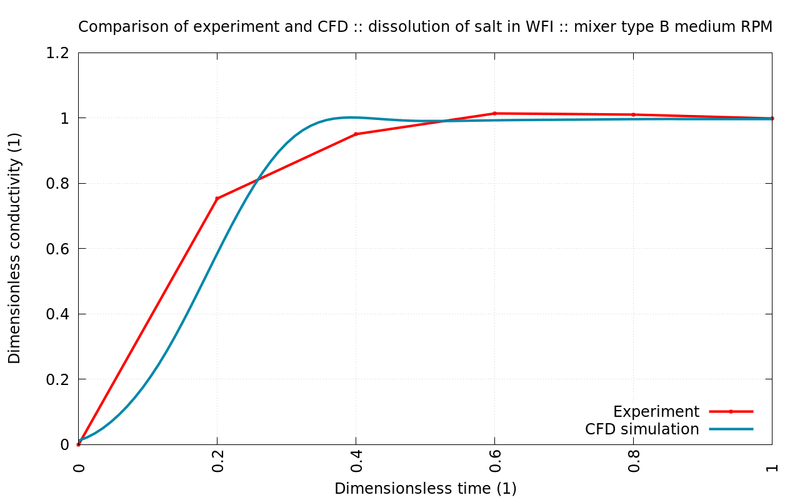
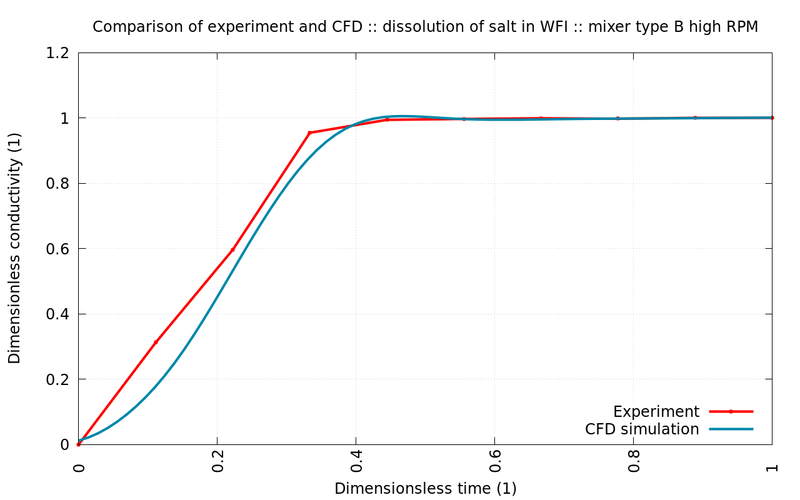
The simulations show excellent agreement with control experiments. Since not only the mixing time but also the shear stresses (not shown) were well within the regulatory boundaries, the engineering team could proceed with high confidence and without the need to costly experiments with plasma or similarly expensive substances.
If you’d like to know what we can do for your case, contact us! We are happy to take a look at your project. The first consultation is always free!
Published: